Active explosion protection systems
Explosion suppression HRD (High Rate Discharge) Fike
Active systems of explosion suppression HRD type (High Rate Discharge). VALWO safety offers wide range of technical consultancy and designing of explosion protection systems, calculation and supplying with assembly and later maintenance. Also we offer service (we are keeping a warehouse of replacement parts, available 24/7, 365/year).
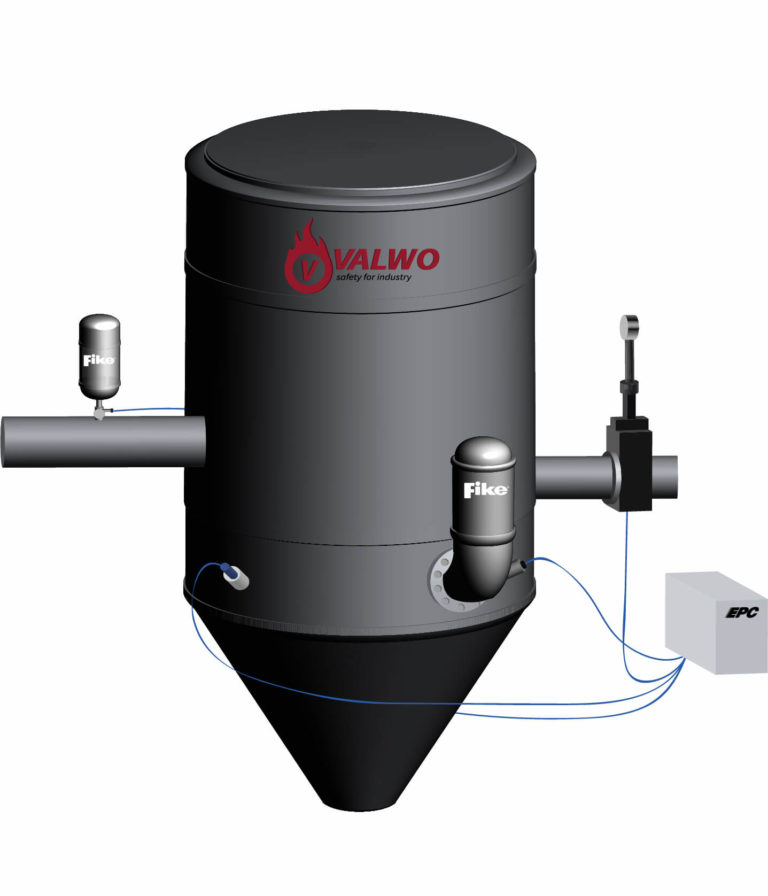
Isolation barrier SRD Fike
Isolation barriers, explosion decouplingnsystems. When a blast wave shifts towards the instalation, a powder is released under high pressure. It’s task is to stop the explosion propagation throw the instalation.
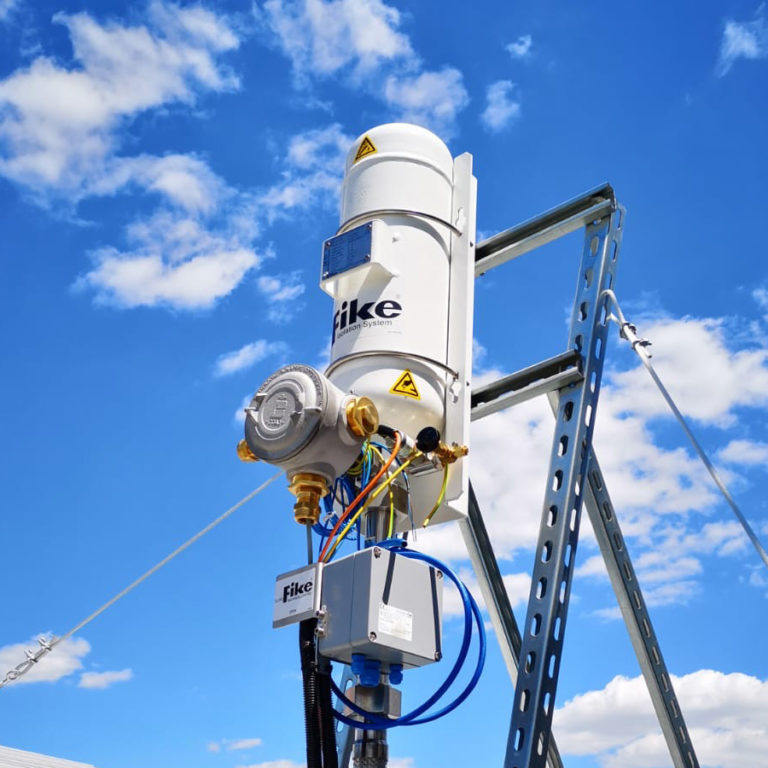
FAV - Fast Acting Valve
Isolating the explosion at the very first stage.
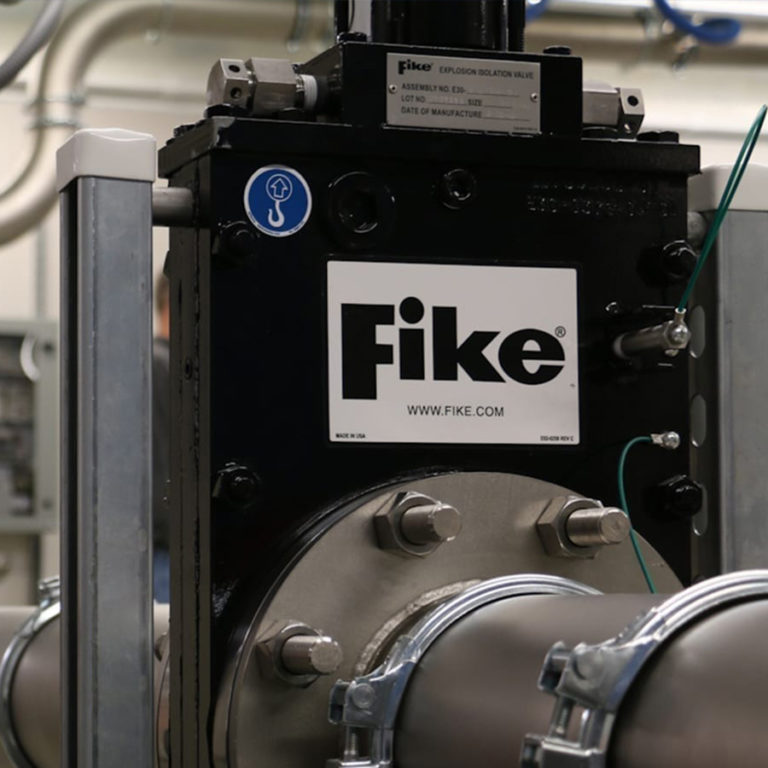
EPACO - Control Cabinet Explosion Protection System
Unit equiped with active suppression and decoupling systems control cabinet, accordingly to configuration, it's characterized by appropriate SIL degree of reliability and additionally it's approved by FM Global.
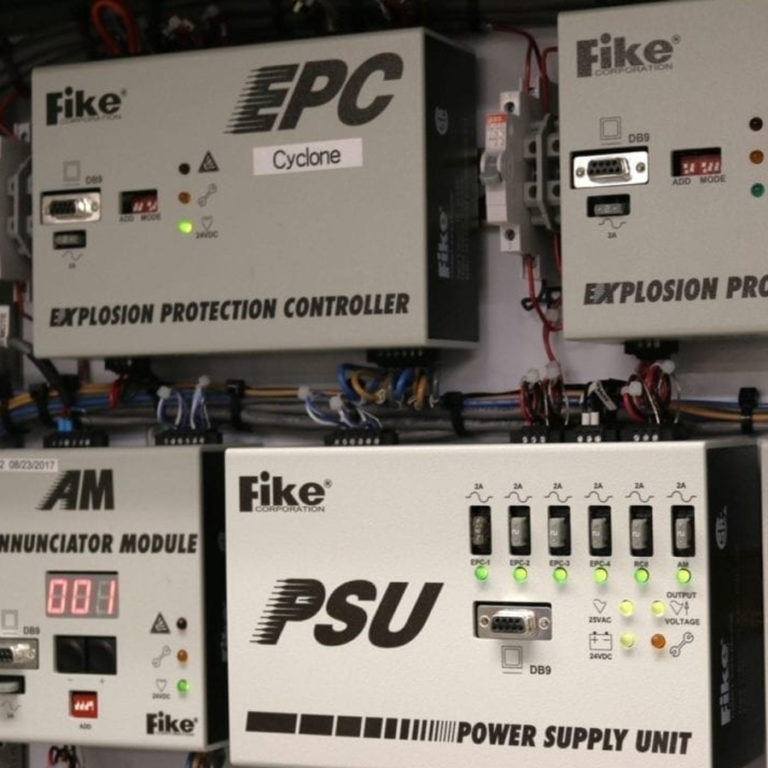
Cerex and Irex transmitter
Pressure detection at the very beginning and passing the information to the controlling unit EPACO to stop the explosion.
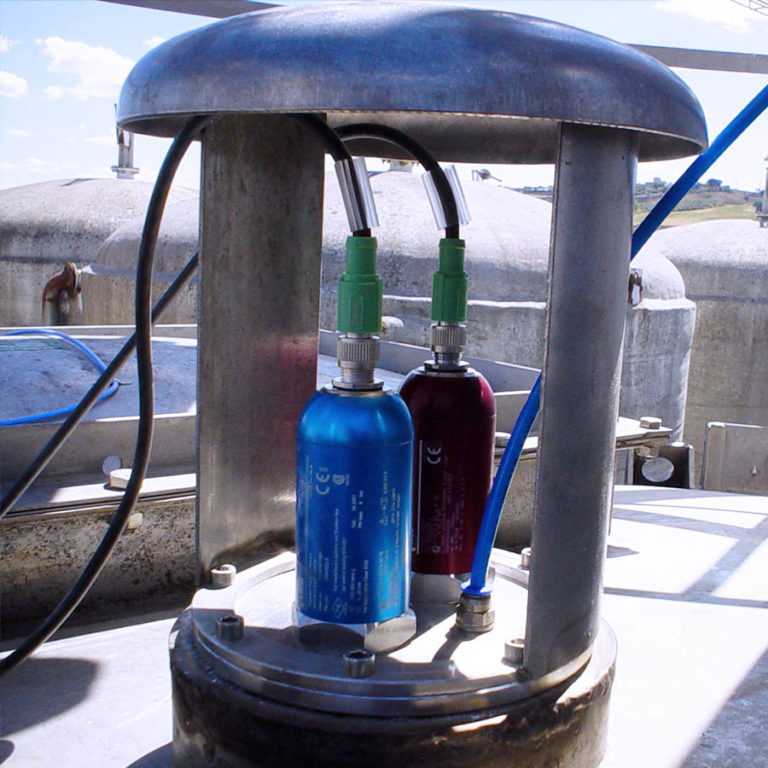
Fike Corporation was established in 1945, USA
The headquarter is places at Blue Springs, Missouri. From the beginning company was focused on implementation of industrial explosion and fire protection systems, based on gained experience.
Since that time, many branches have been launched all over the world (Belgium, France, Germany, Italy, Great Britain, Spain, Canada, Japan, Brazil, India, Bahrain, Malaysia.
In Czech Republic, official representative of Fike is VALWO s.r.o.
The most recognized Fike products are rupture panels and bursting disc (explosion venting), active protection systems against explosion (HRD/SRD) and passive – such as flame quencher (flameless venting) or other modern solutions, as pinch valves or fast activating valves. Common feature of all the equipment is, beside increasing the level of safety, significant increase of economic aspects – lowering the exploitation costs.